自動化提案
FACTORY AUTOMATION
お客様のご要望や
時代のニーズにあった提案を行い、
設備導入後のメンテナンス・ 改善まで
幅広くサポート
自社にて設備構構想を行い、その時その時での最適な提案を行います。導入後も改善対応が必要となるパーツフィーダーや画像検査等は自社にて選定・提案・設定を行うことで、設備導入後も責任持って設備立ち上げに取り組んでおります。
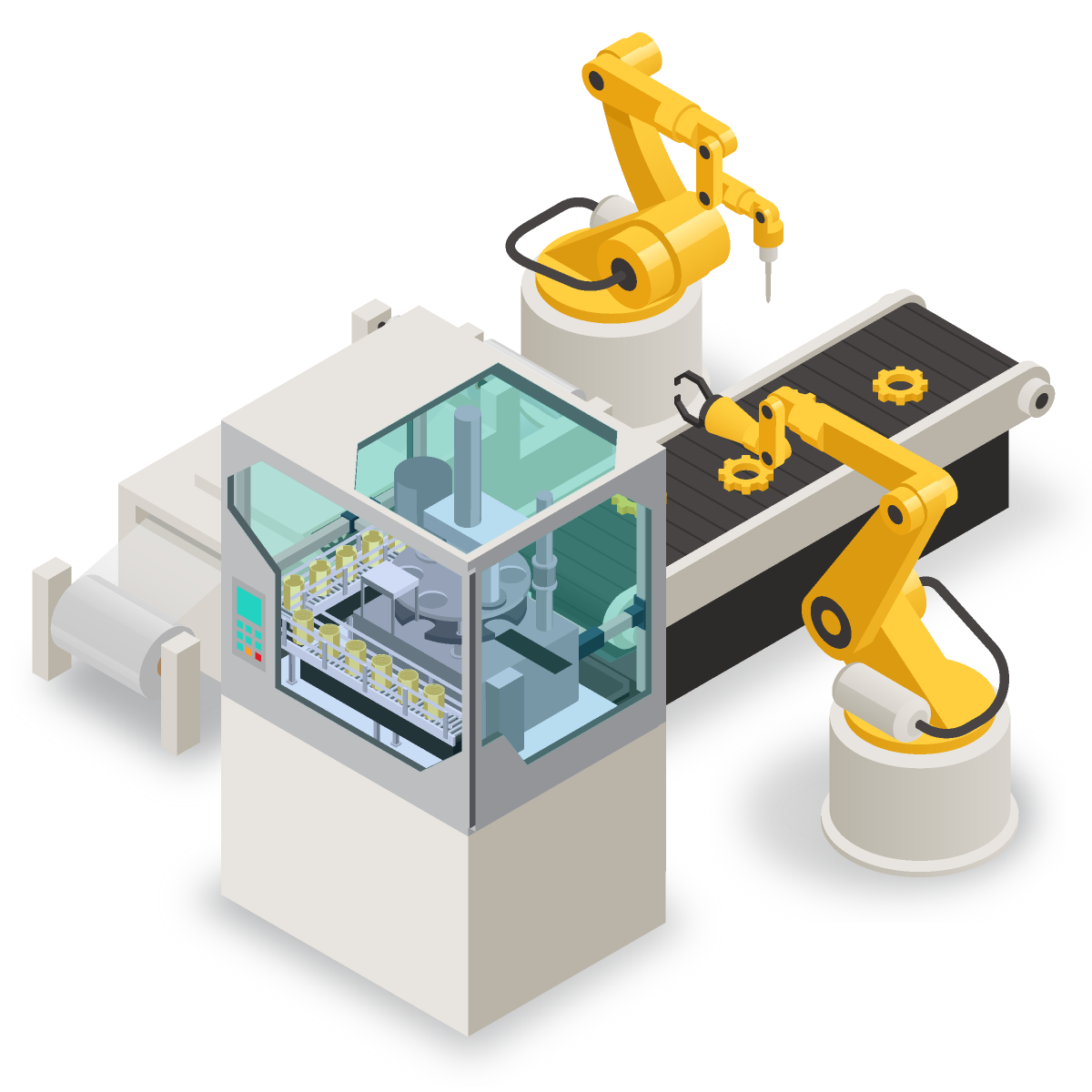
アルファスの強み
- ご要望に合わせた設備構想提案を自社で行い、最適な設備提案をいたします。
- 新たな技術・機構等を日々リサーチし、最新技術の取り込んだ設備提案をいたします。
- セットメーカーは大小10社程度とのお付き合いがあるので、ご要望にあった対応メーカーとタイアップいたします。
- 不具合の多いパーツフィーダーは弊社にて提案、フォローを行います。
- 画像検査は、自社にて選定・設定・立上げまでサポートします。
- 自社にて設計対応が可能な為、既存設備の改善設計等の対応をいたします。
具体的なアプローチ
MACHINED PARTS
お客様からのご要望に関係する問題を追求し、問題の本質的な要因一つひとつを把握し、解決し、ゴールへと導きます。
お客様の問題
自動組立装置におけるパーツフィーダーの
チョコ停が多いので、稼働率が上がらない。
フェーズ1
問題の発見
現場の聞き取り
- 現場確認・作業確認
フェーズ2:問題の分析
チョコ停箇所特定
- チョコ停頻度確認
- 部品公差の確認
- 部品材質の確認
- 組立順序の確認
フェーズ3:問題解決の方法
チョコ停リスク比較
- パーツフィーダー選定
- パーツフィーダー姿勢検討
- 静電気の有無確認
- 供給確率の精査
- 切り出し方法検討
フェーズ4:設計デザインレビュー
概略構想
- 基本機械設計
- 詳細機械設計
- 電気設計
- ソフト設計
フェーズ5:製造
工程管理
- 部品調達
- 装置組立
- 配線
- デバック調整
フェーズ6:設備完成
改善立案・実施
- 現場確認・作業確認
- ワーク品質確認
- 工程能力調査
- 静・動的精度確認
フェーズ7:保守・点検
定期点検
- 予防保全
- 他品番追加改造
- サイクルタイムアップ
- 故障対応
- 部品調達