保全
PARTS FEEDER MAINTENANCE
厳しい要求にも応えられる
用途に応じたパーツフィーダーを構築
作業効率の向上、コスト削減といった様々な目的に応じて、パーツフィーダーの選定、製造、切り出し技術の構築までおこないます。
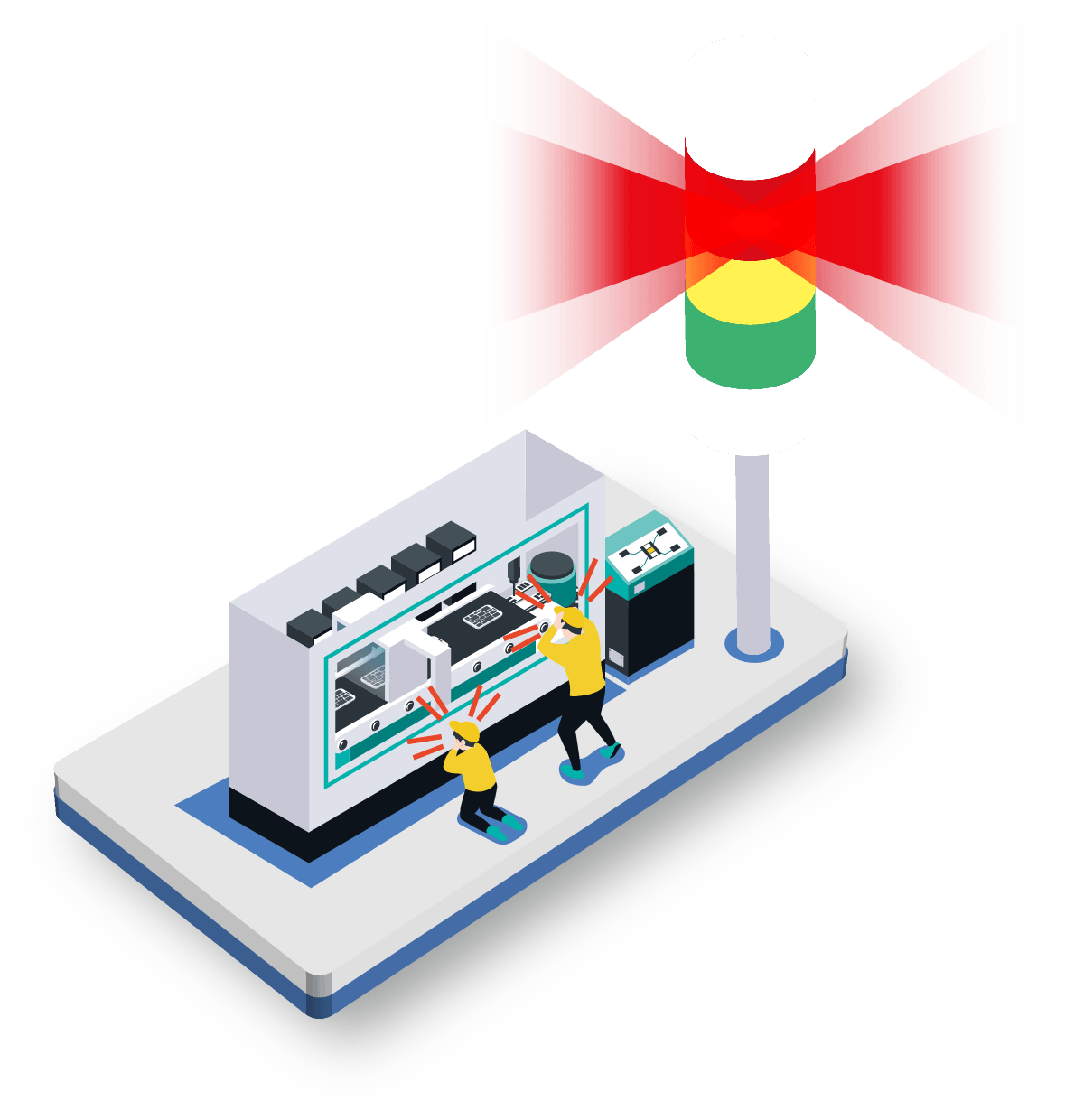
解決できる課題
SOLUTION
メンテナンス・改修コスト・製造ロスにより、チョコ停やドカ停といった表面的なトラブルだけでなく、結果として多くのお客様が多額の支出をしている潜在的な問題があります。
- 自動組立装置の稼働率が上がらない
- 格安で購入した専用機が、想像以上にランニングコストがかかっている
- パーツフィーダーメーカーは、トラブルがあっても来てくれない
- パーツフィーダーメーカーと設備メーカーの技術的なやり取りが、上手くいかない
特徴
PRODUCT FEATURES
パーツフィーダーを導入する前から始める予防保全
トラブルが起こった時に、今までの経験や勘に頼ったその場凌ぎの振動調整では終わらせず、フィーダーの状態を数値化することで、継続した安定稼働の実現はもちろん、対応策の策定や、次回起こりうる問題予測も可能にします。
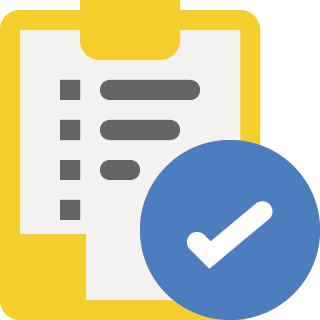
30以上のチェック項目で確認
ボウル・リニア・振動部など、 振動の大きさ、スピード等を計測・記録し、 パーツごとに細かくチェックします。
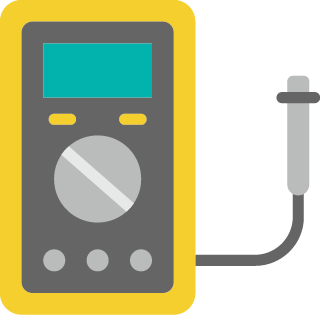
専用計測器で振動を数値化
導入時・現状・改善後、都度計測をおこない、 差異を数値で確認し、定量的に分析します。
コントローラの電圧や周波数に頼らないので、 正確な状態を把握できます。
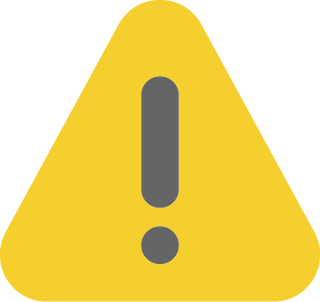
トラブルを未然に回避
対策が必要な場合は、速やかに対応策を提案します。
空転ロスを無くし、 チョコ停の不安を低減します。

PDCA・DXの実行に
安定して稼働しているか、状態をデータ化し、定期的に評価・検証することで、問題点が洗い出せ、次の応用・改善計画が立てやすくなります。
サービスの流れ
FLOW
導入前も後も定期点検を重ねて、安定稼働
導入前に点検項目で正常値を計測することで、安定して稼働する『基準値』を把握します。
導入後は、その『基準値』からどれだけ外れているか計測し、調整する点検を繰り返し実施します。
